Wie bereits im Kapitel «Messkonzepte» geschildert, ist die Erhebung von Messdaten für jedes sinnvolle Energiecontrolling und Energiemanagementsystem unausweichlich. Genauso wichtig sind Messungen für einen optimierten und sicheren Betrieb der gebäudetechnischen Anlagen und deren Überwachung.
Der Automatisierungsgrad in Gebäuden nimmt tendenziell zu. Grössere Gebäude besitzen heute Automationssysteme für Heizung, Ventilation, Klimatisierung, Beleuchtung und Beschattung. Die jeweiligen Teilsysteme sind dabei mit entsprechenden Sensoren und Aktuatoren ausgestattet, die über Bussysteme untereinander kommunizieren und gesteuert bzw. ausgelesen werden können. Zusätzlich sind diese Mess- und Automationssysteme oft an zentrale Datenserver, Webserver und Managementsoftware gekoppelt.
Eine Kenntnis der messtechnischen Grundlagen, der physikalischen Grundprinzipien und der wichtigsten Messgrössen und -geräte bildet die Basis der Handhabung und Realisierung von Messsystemen.
Dieses Kapitel soll einen Überblick über die Grundlagen der Messtechnik vermitteln. Generelle Messtechniken und -anordnungen werden vorgestellt. Die Einbindung fest installierter Messgeräte und Sensoren in ein Messdatenübertragungssystem und die dazu angewandte Netzwerktechnik werden aufgezeigt. Praxisrelevante Begriffe werden erläutert und schliesslich werden die im Energiemanagement wichtigen Messgrössen und Messprinzipien an konkreten Beispielen von Messgeräten anschaulich gemacht.
9.1 Grundlagen der Messtechnik
Zuerst soll verdeutlicht werden, wie physikalische Messgrössen in Messeinrichtungen umgewandelt und auf einfach verständlichen Anzeigen vom Beobachter abgelesen werden können. Die Integration von Messgeräten in grössere Messsysteme wird erklärt und einige der vielen Faktoren identifiziert, welche die Korrektheit eines Messresultats beeinflussen können. In 30, 31 und 32 finden sich ausführlichere Informationen zu den hier erklärten Konzepten sowie weitere wichtige Begriffe der Messtechnik.
9.1.1 Direkte und indirekte Messungen
Direkte Messungen (unmittelbare Messungen) erfolgen, wie ihr Name vermuten lässt, durch das direkte Ablesen einer Messgrösse X anhand eines Messmittels. Ein einfaches Beispiel ist die Längenbestimmung mithilfe eines Massbands. Die Länge L wird durch den unmittelbaren Vergleich mit einem Bezugswert bestimmt.
Gewisse Grössen können hingegen nur schwer oder überhaupt nicht mit einer direkten Messung bestimmt werden. Sie müssen stattdessen indirekt gemessen werden.
Indirekte Messungen (mittelbare Messungen) sind Messungen, bei denen statt der eigentlichen Messgrösse selbst eine Grösse Y gemessen wird, die einen funktionalen Zusammenhang mit der Messgrösse X hat: Y(X). Die mathematische Beschreibung solcher Zusammenhänge wird Modellbildung genannt.
Ein illustratives Beispiel mittelbarer Messgeräte sind Flüssigkeitsthermometer. Das Volumen V der Flüssigkeit im Röhrchen (z.B. Quecksilber) hängt von deren Temperatur T ab: V(T). Da das Glasröhrchen seine Grösse in Abhängigkeit der Temperatur nicht bemerkenswert ändert, kann sich die Flüssigkeit nur entlang einer Dimension ausdehnen. Schlussendlich kann aus der Länge der Flüssigkeitssäule im Röhrchen auf die Temperatur rückgeschlossen werden: L(V(T)).
9.1.2 Messketten, Messeinrichtungen und Messgeräte
Das Beispiel des Flüssigkeitsthermometers ist bereits auch ein Beispiel einer kurzen Messkette. Generell sind Messketten Aneinanderreihungen mehrerer Messschritte. Die Messgrösse wird aufgenommen, weitergeleitet, mehrmals umgeformt und dem Beobachter schliesslich auf einer Anzeige mit Skala oder auf ähnlich komfortable Weise bereitgestellt.
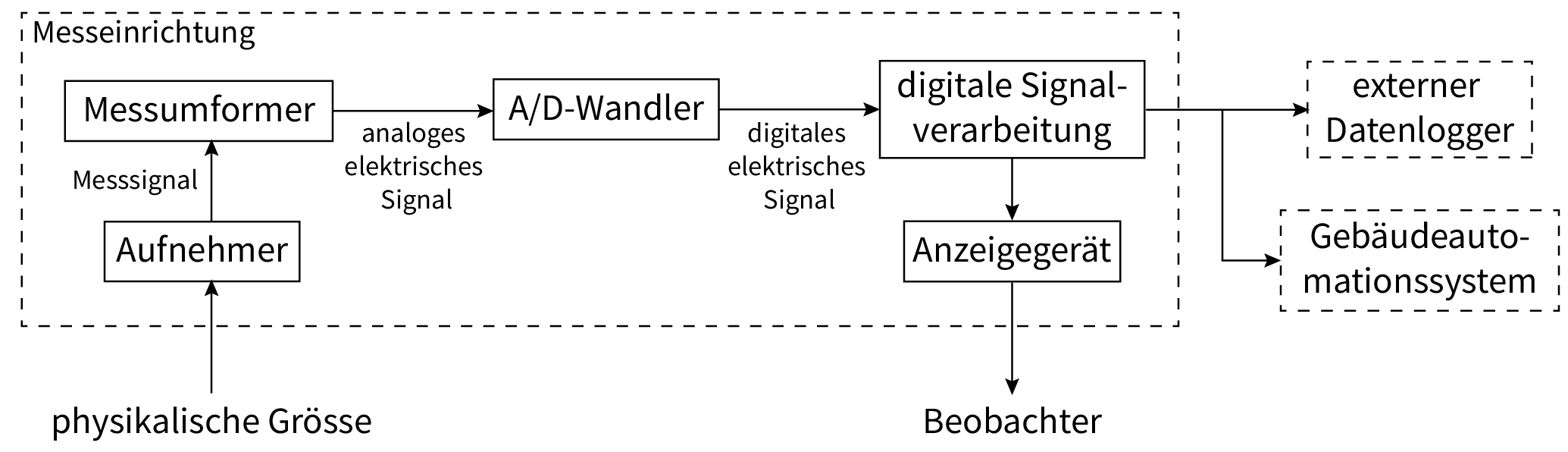
Abb. 42: Schematisches Beispiel einer Messeinrichtung. Die zu messende physikalische Grösse wird aufgenommen, umgeformt, diskretisiert und in digitaler Form weiterverarbeitet. Ein Anzeigegerät zeigt die Messgrösse direkt am Gerät an. Mittels einer entsprechenden Schnittstelle können die Messdaten von externen Geräten ausgelesen werden.
Die Gesamtheit der Messschritte wird als Messeinrichtung oder Messgerät bezeichnet. Solche Messeinrichtungen enthalten meistens Messumformer, welche die Messgrösse in ein elektrisches Signal umwandeln, das ausgelesen, weiterverarbeitet oder auch gespeichert werden kann. Heutzutage ist die (digitale) Signalverarbeitung in Mikrokontrollern oder Computern ein weiterer wesentlicher Bestandteil vieler Messgeräte. Abb. 42 zeigt eine schematische Messeinrichtung mit den genannten Komponenten.
9.1.3 Analoge und digitale Messgeräte
Innerhalb eines Messgeräts kann das Messsignal entweder komplett stufenlos verarbeitet werden, sich nur in diskreten Amplitudenschritten bewegen oder sowohl zeitlich als auch in der Amplitude diskretisiert werden. Im ersten, stufenlosen Fall spricht man von einem analogen Messgerät, in den beiden anderen, quantisierten Fällen von digitalen Messgeräten.
Die beiden Beispiele einer Längenmessung und einer Temperaturmessung in Abb. 43 stellen Fälle einer analogen Messung dar. Die Messwerte liegen auf einer kontinuierlichen Skala vor.

Abb. 43: Beispiele typischer Anzeigeelemente von analogen (links) und digitalen (rechts) Messgeräten. Es gibt gewisse Ausnahmen (z.B. analoge Rollenzählwerke in Induktionszählern), bei denen die Anzeige eine falsche Messgerätfunktion vermuten lassen kann. Zudem gilt zu beachten, dass Messgeräte mit Digitalanzeigen trotz z.B. zusätzlicher Kommastellen nicht unbedingt präziser sind.
Ein einfaches, etwas altmodisches Beispiel digitaler Messgeräte sind Zähler, die nach jedem gemessenen Eingangssignal mittels eines Zählwerks eine Ziffer um einen diskreten Wert weiterbewegen (quantisierte Amplitude).
Mithilfe von Analog/Digital-Wandlern (kurz A/D-Wandler) kann auch ein analoges elektrisches Signal abgetastet und so in ein digitales Signal umgewandelt werden. Eine analoge Messgrösse kann also in ein elektrisches Signal umgewandelt, diskretisiert und als digitalisierte Grösse weiterverarbeitet werden.
Zusammen mit im Messgerät integrierten Mikroprozessoren können die digitalisierten Messdaten beispielsweise in Zahlenform auf einem LCD (liquid crystal display) oder Ähnlichem angezeigt werden. Alternativ werden die Daten in interne Speicher geschrieben, wo sie zu einem späteren Zeitpunkt über eine Schnittstelle wieder ausgelesen werden können, oder sie werden mit einem Datenübertragungsmodul über ein entsprechendes Kommunikationsprotokoll an weitere externe Geräte gesendet – sei dies eine kleine externe Platine mit Prozessor, ein Smartphone, ein Laptop, ein lokaler Datenserver oder ein Webserver.
9.1.4 Vernetzte Mess- und Automationssysteme in Gebäuden
Aufgrund ihrer Kosteneffizienz, Grösse und Genauigkeit werden in Gebäudeautomationssystemen und Messsystemen zunehmend Messgeräte installiert, die lediglich Messgrössen erfassen und über Datenbusse übertragen können.
Ein Bus ist ein Datenübertragungssystem, das die Kommunikation zwischen mehreren Teilnehmenden auf nur einem Übertragungsweg regelt. Wenn Messgerät A dem Buskontroller Messdaten übermitteln will, kann Messgerät B nicht gleichzeitig seine Messdaten auf derselben Busleitung übertragen, ohne die Kommunikation zwischen A und dem Buskontroller zu stören. Die reibungslose und verlustfreie Datenübertragung wird durch ein entsprechendes Busprotokoll geregelt. Dieses definiert, zu welchem Zeitpunkt welcher Teilnehmer die Sprechberechtigung auf der gemeinsamen Leitung besitzt.
In der konkreten technischen Umsetzung eines Busprotokolls besteht sehr viel Freiheit. Gebräuchliche Beispiele von Busprotokollen auf der Feldbusebene in Messsystemen und in der Gebäudesystemtechnik sind M-Bus, EIB/KNX und LON. Diese Busprotokolle können sowohl auf drahtgebundenen als auch auf drahtlosen Übertragungswegen eingesetzt werden.
Abb. 44 zeigt ein Beispiel eines Messbusnetzwerks. Zuunterst, auf der Feldebene, kommunizieren einzelne Messgeräte über eine Busschnittstelle mit dem Buscontroller, bzw. dem Gateway zur nächsten Ebene des Messsystems. Auf dem Markt finden sich hier verschiedenste Geräte zur Implementierung und Anbindung von Feldbussystemen. Feldbusse können damit selbst mehrere Untergruppen besitzen, die sowohl kabelgebunden (Twisted-Pair-Kabel, manchmal mit Standard-Netzwerksteckern) als auch via Funk kommunizieren können. Wie im Kapitel «Messkonzepte» beschrieben, können Bussysteme in verschiedenen Netzwerktopologien realisiert werden.
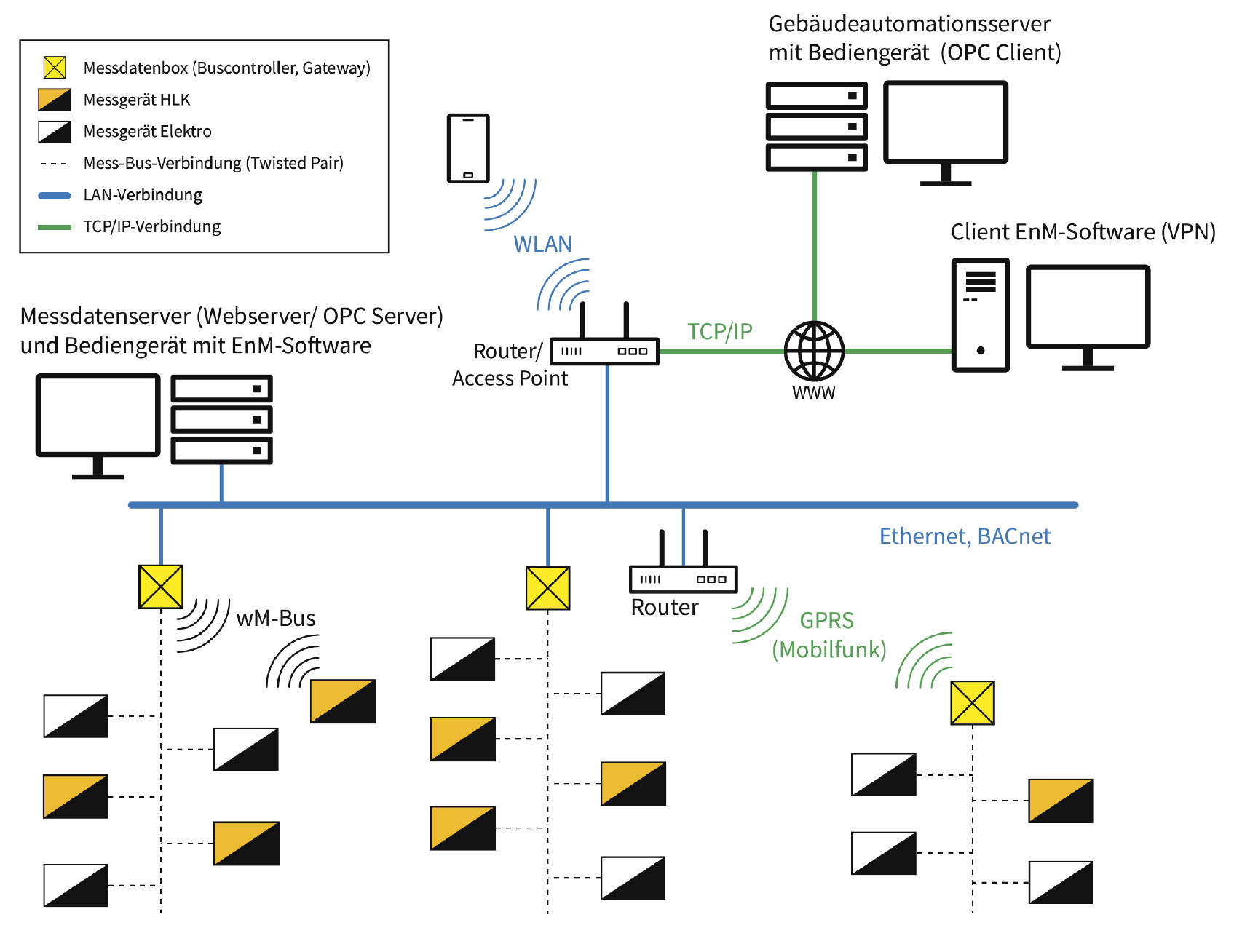
Abb. 44: Beispiel eines Messsystems
Der Buscontroller selbst verfügt normalerweise über eine Schnittstelle zur Anbindung an ein LAN (Ethernet, in der Gebäudesystemtechnik auch oft BACnet). Gewisse Controller implementieren zusätzlich GPRS-Gateways, haben Routingfähigkeiten (TCP/IP) oder hosten einen eigenen Webserver, um Messdaten direkt über das Netzwerk im Webbrowser auszulesen. Manche Geräte nutzen auch LPWANs (low-power wide-area networks) zur Messdatenübertragung, wie beispielsweise LoRaWAN. Mit diesen günstigen, energieeffizienten Drahtlos-Netzwerken können Messgeräte über mehrere Kilometer kommunizieren, ohne Gateways nutzen zu müssen.
Innerhalb des lokalen Netzwerks können die Messdaten über ein (mobiles) Bediengerät mit entsprechender Software eingesehen oder beispielsweise auf einem Server gespeichert werden. Ein Messdatenserver kann zusätzlich einen Webserver hosten oder die Messdaten via OPC (Open Platform Communications) einem externen OPC-Client zur Verfügung stellen. Die OPC-Standards wurden entwickelt, um den Datenaustausch zwischen Anwendungen vieler verschiedener Hersteller von automationstechnischen Geräten zu regeln. Bilden verschiedene Sensoren und Steuerungen von verschiedenen Herstellern ein gemeinsames Netzwerk, werden mit OPC die entsprechenden Daten vereinheitlicht.
Letztlich kann das lokale Netz mit einem TCP/IP-Router an das Internet angeschlossen werden.
9.1.5 Messabweichungen
Ein Messwert kann aus verschiedensten Gründen vom wahren physikalischen Wert abweichen. Deshalb muss in der Praxis das Resultat einer Messung immer mit einer gewissen Skepsis betrachtet werden. Wurde das Messgerät korrekt bedient? Ist die Messung präzis? Und ist die Messanordnung überhaupt sinnvoll?
Die Abweichung des Messwerts vom wahren Wert besteht aus der Messabweichung und der Messunsicherheit. In Abb. 45 sind die wichtigsten Komponenten von Messabweichungen visualisiert.
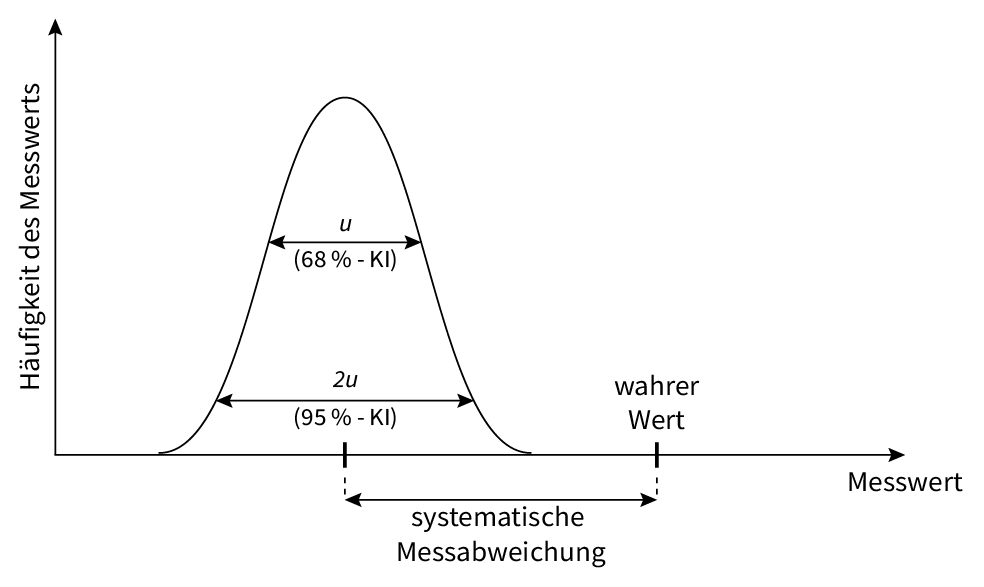
Abb. 45: Illustration der Messabweichung, die sich aus einer systematischen und einer zufälligen Komponente zusammensetzt. Die zufällige Messabweichung ist normalverteilt und die Konfidenzintervalle der Standardunsicherheit u und der erweiterten Unsicherheit 2u sind gezeigt.
Die Messabweichung bezeichnet die Differenz zwischen Messwert und dem realen physikalischen Wert. Die Abweichung kann verschiedene, mehr oder weniger problematische Ursachen haben. Die Art der Messabweichung fällt üblicherweise in eine der folgenden Kategorien.
Grobe Messfehler
Grobe Messfehler entstehen bei schlechten Messbedingungen, falscher Bedienung eines Messgeräts, Störungen und Defekten im Messgerät oder bei der Messdatenübertragung. Beispiele wären der Versuch, die Raumtemperatur direkt neben einem Heizelement zu messen, oder das Setzen eines falschen Parameters, z.B. der Wärmekapazität in einem Wärmezähler. Diese Messfehler sind grundsätzlich durch korrekte Handhabung des Geräts vermeidbar.
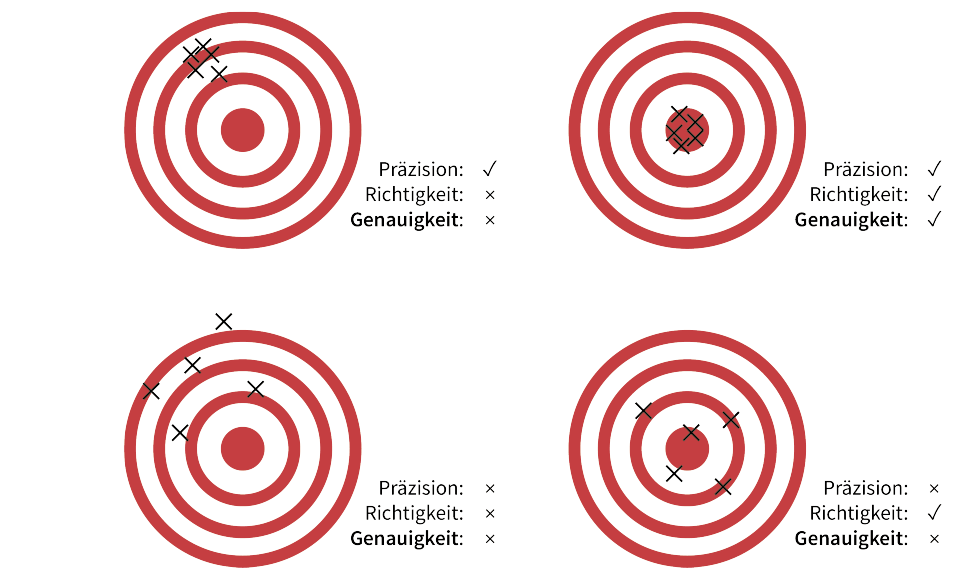
Abb. 46: Visualisierung des Begriffs der Genauigkeit. Genauigkeit setzt sich aus Präzision und Richtigkeit zusammen. Nur Messungen, die sowohl präzise als auch richtig sind, sind genaue Messungen.
Systematische Messabweichungen
Systematische Messfehler sind konstante Messabweichungen. Das Messresultat ist vom wahren Wert mit gleichbleibendem Vorzeichen und Betrag verschieden. Wiederholtes Messen derselben Grösse unter den gleichen Bedingungen liefert dasselbe Ergebnis, weshalb systematische Messfehler schwer zu identifizieren sind. Die Ursache systematischer Messabweichungen findet sich bei Ungenauigkeiten in der Messeinrichtung oder bei Mangeln im Messverfahren.
Eine weitere Quelle systematischer Messfehler ist eine Rückwirkung des Messvorgangs auf die Messgrösse selbst. Beispielsweise wird durch den Innenwiderstand eines Voltmeters die zu messende Spannung verändert.
Durch Vergleich mit einem genaueren, geeichten Messgerät lässt sich die Messgeräteabweichung jedes Messgeräts bestimmen. So kann eine Fehlerkurve des Messgeräts bestimmt werden, die aufzeigt, wie stark das Messresultat vom wahren Wert im jeweiligen Wertebereich abweicht. Als Beispiel sind Thermistoren (temperaturabhängige elektrische Widerstände) nur in gewissen Wertebereichen linear von der Temperatur abhängig. Sind die systematischen Abweichung eines Messgeräts bekannt, können sie durch Umrechnung kompensiert werden.
Zufällige Messabweichungen
Wie der Name schon sagt, sind zufällige Messabweichungen im Gegensatz zu systematischen Messabweichungen nicht konstant. Bei wiederholter Messung, selbst unter scheinbar exakt denselben Bedingungen, streuen sich die Messresultate. Sie finden ihre Ursache in kleinen, nicht beherrschbaren Schwankungen der Messgrösse, der Messbedingungen, des Messgerätes oder in Einflüssen des messenden Beobachters (z.B. nicht perfektes Ablesen einer Skala).
Oft sind zufällige Messabweichungen normalverteilt und können mittels Fehlerrechnung aus einer genug grossen Anzahl Messungen abgeschätzt werden.
Sonderfälle
Ein Sonderfall von Messabweichungen sind einerseits dynamische Messabweichungen, die sich also zeitlich ändern. Nach Eingang einer neuen physikalischen Grösse verzögert sich die Anzeige des korrekten Resultats oder gleicht sich ihm nur langsam an. Ein Beispiel hierfür ist die Messung einer Partikelkonzentration (z.B. CO2 oder Radon) in einem neuen Raum. Messgeräte mit dynamischen Messabweichungen benötigen eine gewisse Zeitspanne, um einen neuen Wert vom Eingang zum Ausgang zu propagieren.
Speziell im Hinblick auf digitale Messgeräte sind Quantisierungsabweichungen ein weiterer Spezialfall von Messabweichungen. Sie entstehen bei der Quantisierung analoger Grössen. Analoge Signale können jeden beliebigen Wert annehmen und sich kontinuierlich im Wertebereich der reellen Zahlen verändern; digitale Signale nehmen hingegen nur diskrete Werte an. Eine Analog/Digital-Umwandlung entspricht also einer Rundung und der resultierende Rundungsfehler entspricht der Quantisierungsabweichung. In Abb. 47 ist die Diskretisierung eines analogen Signals zusammen mit der resultierenden Messabweichung gezeigt.
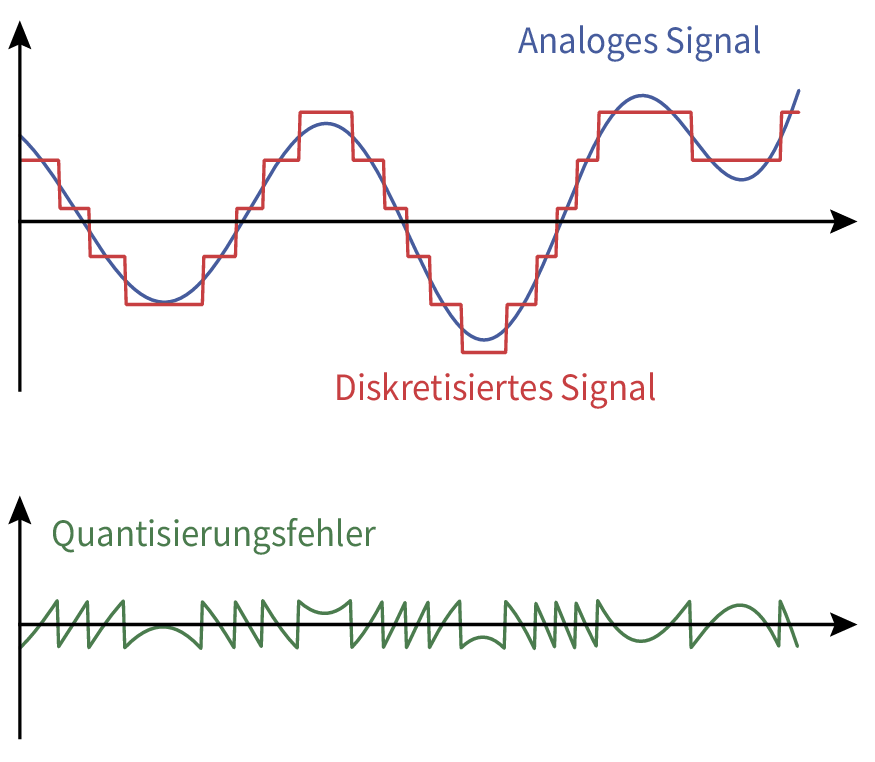
Abb. 47: Quantisierung eines analogen Messsignals (oben). Der resultierende Quantisierungsfehler (unten) trägt zur Messabweichung bei.
9.1.6 Messunsicherheiten
Die Messunsicherheit dient zur Eingrenzung des Wertebereichs, innerhalb dessen sich der wahre Wert mit einer angegebenen Wahrscheinlichkeit befindet. Sie beschreibt also die Streuung der zufälligen Komponente der Messabweichung.
Wie bereits erwähnt, sind zufällige Messabweichungen oft normalverteilt, weshalb meist entweder die Standardunsicherheit u (68%-Konfidenzintervall) oder die erweiterte Unsicherheit 2u (95%-Konfidenzintervall) als Messunsicherheit angegeben werden. Eine Angabe wie 27,6575 ± 0,0054 ist nicht sehr hilfreich, wenn nicht ausdrücklich erklärt wird, wofür die nach «±» angegebene Grösse steht.
Zu einem aussagekräftigen Messresultat gehört deshalb eine klare Angabe der Messunsicherheit, denn sie erlaubt es erst, den angegebenen Messwert zu objektivieren. Auf einem Digitaldisplay wird beispielsweise der Wert 2,612 angezeigt. Dieser Wert allein kann stark irreführend sein und lässt in dieser Form auf vermeintlich hohe Präzision schliessen. Wenn die Messunsicherheit aber u = 0,1 beträgt, sind die zusätzlichen Nachkommastellen reine Dekoration.
Auch in der Definition der Anforderungen an ein einzusetzendes Messgerät sollten immer die tolerierbaren Messunsicherheiten enthalten sein. Ein genaueres Messgerät bringt gewöhnlich höhere Kosten mit sich. Deswegen gilt hier zu hinterfragen, ob es beispielsweise wirklich nötig ist, eine Verbraucherleistung im Sekundentakt und mit hoher Präzision zu messen, wenn eine weniger präzise Messung im Fünfzehnminutentakt im gleichen Mass zielführend wäre.
9.1.7 Justierung, Kalibrierung und Eichung
Die Begriffe Justieren, Kalibrieren und Eichen liegen nahe beieinander und werden daher auch oft verwechselt.
Justieren bezeichnet das Einstellen eines Messgerätes mit dem Ziel, systematische Messabweichungen zu korrigieren. Eine Nachjustierung kann bei bestimmten Messgeräten regelmässig notwendig sein. Oft können Geräte vom Messenden selbst justiert werden. So kann ein Messgerät beispielsweise mit einer Vergleichsmessung eines besseren Messgeräts justiert werden, oder indem eine bekannte Grösse gemessen wird (z.B. Eiswasser mit 0 °C Temperatur oder gesättigte Luft mit 100% relativer Feuchte).
Kalibrieren ist die Bestimmung des Zusammenhangs zwischen Anzeige des Messgerätes und dem wahren Wert über den gesamten Messbereich. Dies erfolgt meist durch Vergleich mit einer zweiten, vertrauenswürdigeren Messung (z.B. mit einem geeichten Messgerät) oder im Labor. Die Kalibrierung kann bei genügender Fachkompetenz selbst vorgenommen werden oder erfolgt z.B. durch den Gerätehersteller im Rahmen eines Service.
Eichen ist das Kalibrieren durch amtliche Institutionen (kantonale Eichämter) oder durch ermächtigte Eichstellen. In der Schweiz beaufsichtigt das Eidgenössische Institut für Metrologie (METAS) sämtliche Eichstellen und betreibt zusätzlich auch einen eigenen Eichdienst.
Bei bestimmten Messeinrichtungen, wie z.B. Energiezählern zur Abrechnung des Energieverbrauchs, kann eine Eichung vorgeschrieben sein. Eichpflichtige Messgeräte benötigen eine amtliche Zulassung mit Konformitätsbewertung und einer Bauartprüfung. Sie müssen den zuständigen Eichämtern gemeldet werden.
Die Ersteichung erfolgt typischerweise durch das METAS. Erforderliche Nacheichungen werden typischerweise von kantonalen Eichstellen gehandhabt. Sie werden durch einen Kleber (Abb. 48) bestätigt, der auf die nächstfällige Nacheichung verweist.
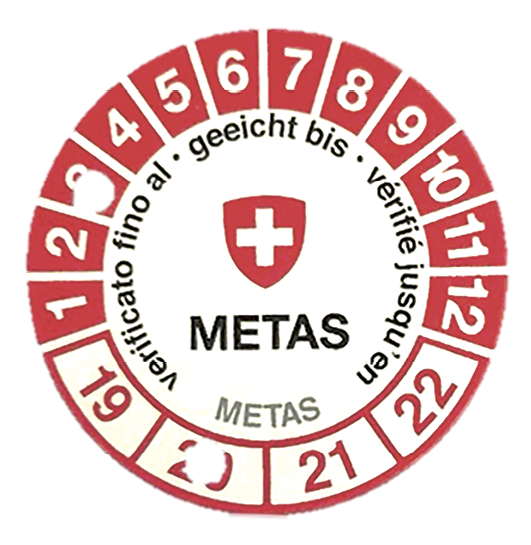
Abb. 48: Eichmarke des METAS, gültig bis März 2020
Eidgenössisches Institut für Metrologie METAS
9.1.8 Praktische Anforderungen an Messgeräte
Abhängig vom Einsatzgebiet eines Messgeräts, ist es diversen äusseren Einflüssen wie Feuchtigkeit, Temperatur, Staub und mechanischen Krafteinwirkungen ausgesetzt. Soll das Messgerät seine Funktion wie vorgesehen erfüllen, muss es durch ein Gehäuse im entsprechenden Mass geschützt sein. Die Gehäuseschutzart ist in ISO 20653 und EN 60529 festgelegt und wird mit der zweistellige IP-Kennziffer angegeben (Tab. 6 und Tab. 7). Die erste Ziffer bezeichnet dabei den Schutz gegen feste Fremdkörper (wie z.B. Staub), die zweite Ziffer den Schutz gegen Wasser und Feuchtigkeit.
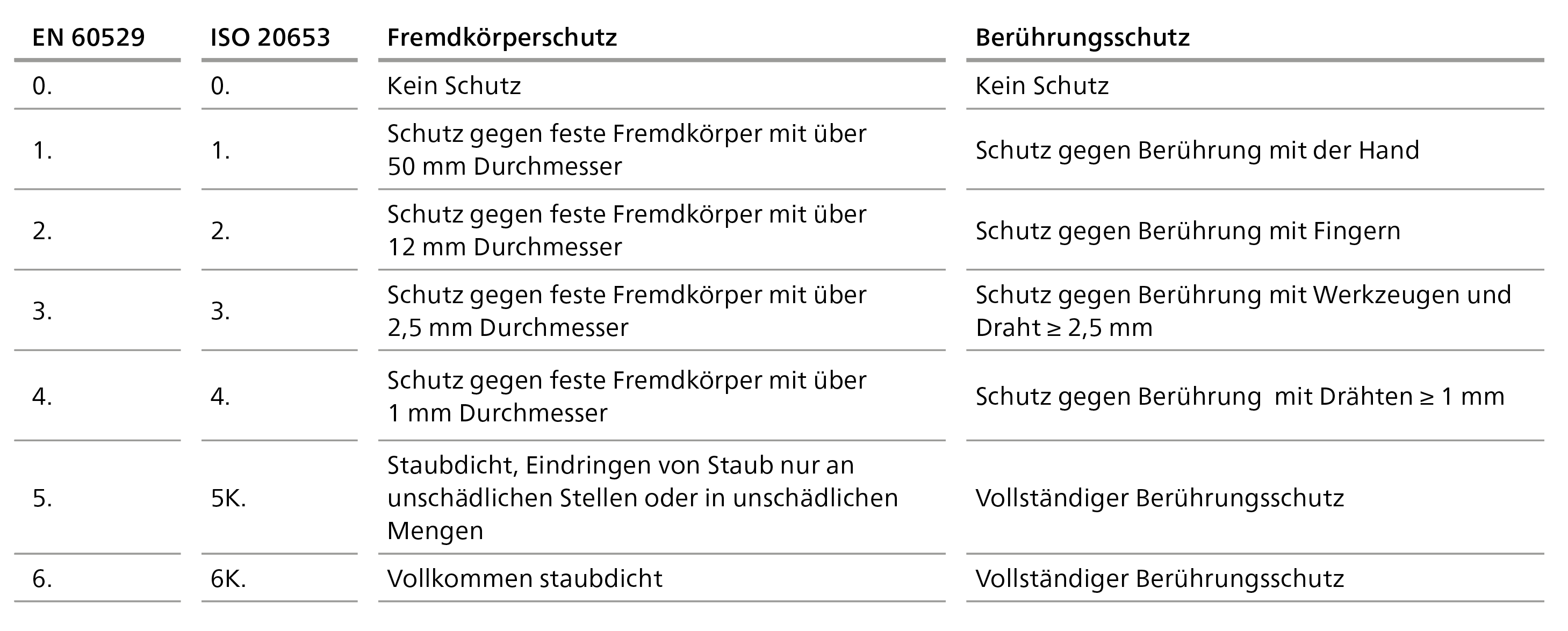
Tab. 6: IP-Schutzkodierung, 1. Kennziffer
.
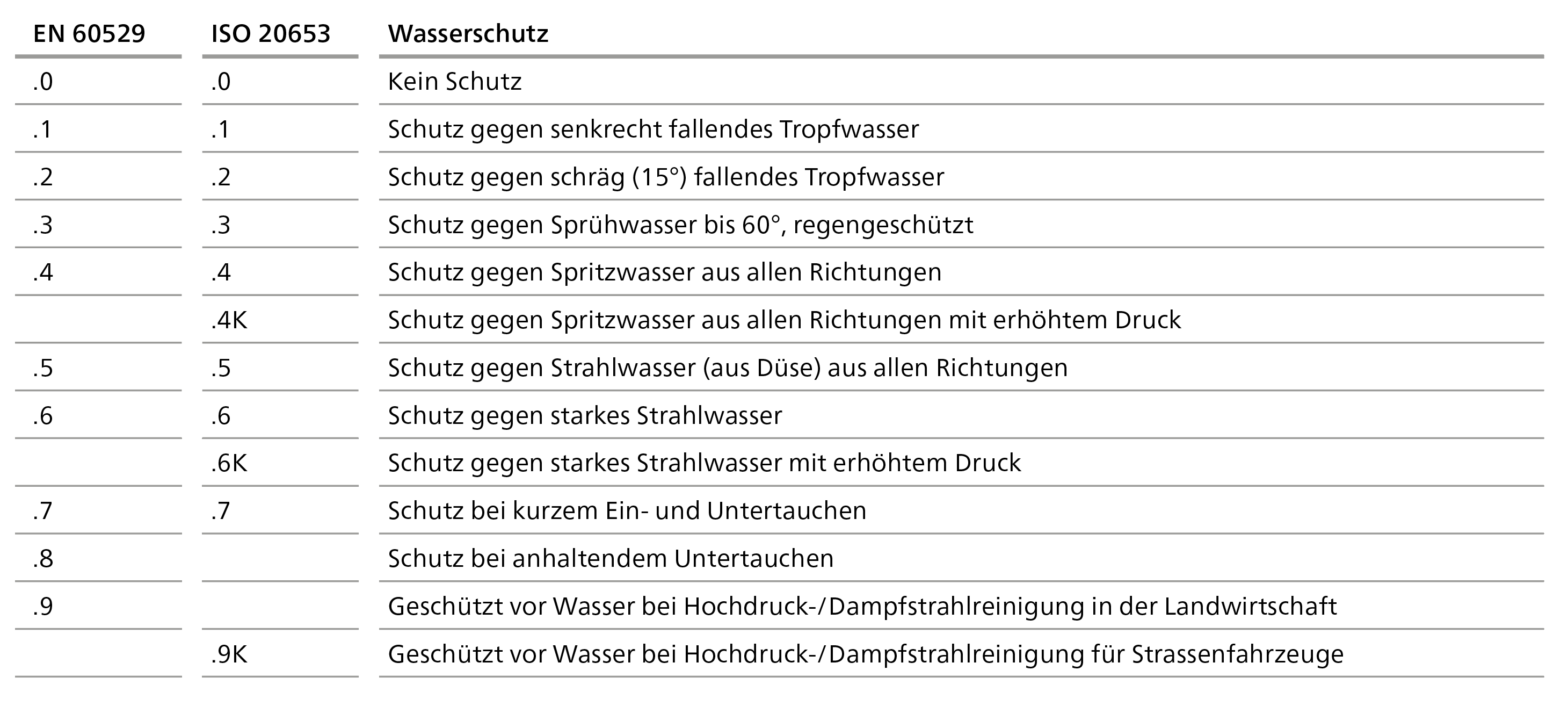
Tab. 7: IP-Schutzkodierung, 2. Kennziffer
Die Schutzart gegen mechanische Krafteinwirkung (Stossfestigkeit) wird mit den IK-Codes (Tab. 8) angegeben und ist gemäss EN 50102 resp. IEC 62262 festgelegt. Gemessen wird die Aufschlagenergie eines Schlages mit einem Hammer.
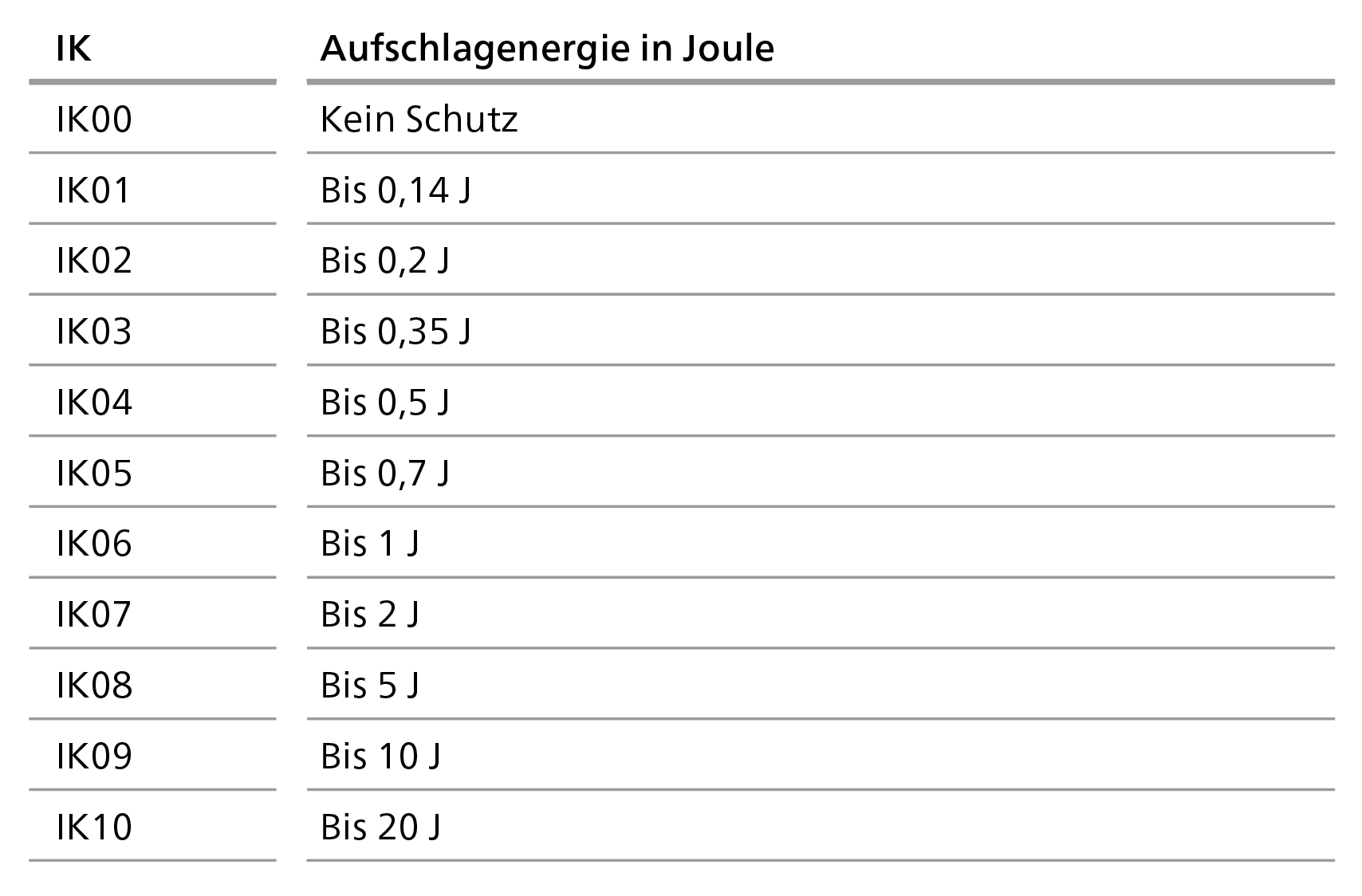
Tab. 8: IK-Schutzkodierung
Messgeräte, die in explosionsgefährdeten Zonen (Gas- oder Staubexplosionen) eingesetzt werden, wie in Benzintanks oder Holzschnitzelsilos, dürfen nachvollziehbar auf keinen Fall Zündquellen erzeugen. Dies wird durch einen entsprechenden Konstruktionsstandard sichergestellt und ist in weiteren europäischen Normen festgelegt. Bei elektrischen Geräten sind die Explosionsschutzmassnahmen als Zündschutzarten definiert. In gasexplosionsgefährdeten Bereichen werden beispielsweise Strom und Spannung im Gerät begrenzt, um so eine Überschreitung der Zündgrenzwerte zu vermeiden (Zündschutzart der Eigensicherheit «Ex i»). Alternativ kann verhindert werden, dass eine Explosion im Inneren des Geräts nach aussen gelangt (Zündschutzart der druckfesten Kapselung «Ex d»).
Die verschiedenen Explosionsschutzarten sind in der Normenreihe EN 60079-ff definiert. Für Messgeräte, die in explosionsgefährdeten Zonen eingesetzt werden, ist eine Konformitätserklärung nach der Verordnung über «Geräte und Schutzsysteme zur Verwendung in explosionsgefährdeten Bereichen» (VGSEB) zu verlangen, entsprechend der Richtlinie 2014/34/EU über «Geräte und Schutzsysteme zur bestimmungsgemässen Verwendung in explosionsgefährdeten Bereichen» (ATEX95).